Heat pumps
Principle and architecture of the heat pump
In refrigeration cycles, the practical effect is the extraction of heat by the evaporator. We can also design a machine whose useful effect is heating by waste heat available in the condenser. We call such a machine a heat pump, whose cycle is very similar to that used in refrigeration. It differs only by temperature levels, and therefore the working fluid.
Consider a situation where we have simultaneously thermal needs at average temperature (e.g. 50 ° C), and a "free" heat source at a temperature slightly lower than that of needs (e.g. 10 ° C).
The principle (Figure below) is to evaporate a refrigerant at low pressure (and therefore low temperature) in a heat exchanger in contact with the cold source. For this, we need temperature Tevap of the refrigerant to be lower than that of the cold source Tef. The fluid is then compressed at a pressure such that its condensation temperature Tcond is greater than the temperature of needs Tn. It is then possible to cool the fluid by heat exchange with the thermal needs until it becomes liquid. The liquid is then expanded at low pressure by isenthalpic throttling, and directed into the evaporator. The cycle is thus closed.
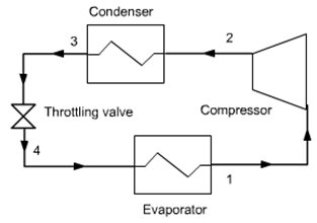
Figure below illustrates the enthalpy transfers that take place in the facility. Small arrows pointing downwards represent the heat exchange, which, as can be seen, do not infringe the Second Law of thermodynamics, heat flowing from warmer areas to colder areas.
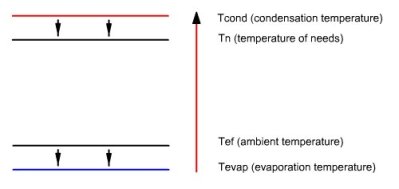
The long upwards arrow represents the enthalpy contribution of the compressor, which can raise the temperature of the fluid (note: the amounts of heat are not proportional to the length of arrows).
The effectiveness of such a cycle is defined as the ratio of useful energy to purchased energy. Thus it is the ratio of heat extracted from condensor to compressor work. Because its value is generally greater than 1, we prefer to speak of Coefficient of Performance or COP.
For a heat pump, we define a heating COefficient of Performance COPh. Indeed, the First Law states that all the energies involved are discharged at the condenser, that is to say, the heat energy taken from the cold source plus the mechanical energy of compression.
COPh = = 1 + COPrefrig
Heat pumps can raise the level of temperature of a cold source with excellent efficiency, as long as the temperature difference is not too important.
This heating method is very attractive if one has a source of free heat at a sufficient temperature. For space heating, it has one drawback: the COPh decreases gradually as the heating needs are increasing, as the temperature difference between the cold source and heating system increases simultaneously.
Heat pumps are used not only for space heating but also for various industrial applications. Other uses such as cooling of ice coupled to heating a public swimming pool make use of both the cooling and the heating functions.
Components
In terms of thermodynamics, a heat pump is composed of four elements.
The explanations below refer specifically to those used for space heating.
The evaporator which extracts heat from the cold source. It can be done in different ways depending on the cold source used. In the case of the outside air, it is often a coil of finned tubes inside which flows the working fluid, air flowing outside. If it is a river, it can be a plate or shell and tube heat exchanger, or simply a co-axial coil. This evaporator is connected to the rest of the machine by two pipes which pass through the housing walls. One of them is connected to the compressor suction, the other to the expansion valve;
The condenser is the heat exchanger which transfers heat removed to the environment to the heating system. It can also be a plate or shell and tube heat exchanger, or a co-axial coil. It is connected to the compressor outlet and expansion valve;
In most cases, the displacement or centrifugal compressor is not directly visible because it is contained in a metal block mounted on rubber cushions to prevent vibrations, out of which exit an electric wire and two input and output fluid pipes. Such a compressor, generally of piston type, is called a hermetic compressor, which has the advantage that the engine is directly cooled and lubricated by the working fluid, without need for oil;
The expansion valve usually consists of a single capillary tube, and sometimes is a thermostatic valve. Before entering the valve, the liquid is slightly subcooled, this ensures that the body is not supplied with vapor, and this increases the performance of the machine.
Industrial applications
Heat pump applications in industry are as follows, Te and Tc being respectively the temperatures of evaporation and condensation:
Te < 20 °C, Tc < 80 °C: standard conventional heat pumps, marketed and available in a catalog;
20 °C < Te < 80 °C, Tc < 130 °C: specific heat pumps, though derived from refrigeration equipment, but adapted to higher operating temperatures;
for higher temperatures, such material is no longer appropriate. Mechanical vapor compression may be a solution, if the cold source is in the form of vapor.
Compressors used in practice are of three types: reciprocating (P <200 kW), screw (100 kW <P <1 MW), or centrifugal (P> 800 kW).
Currently, the main markets for heat pumps in industry concern drying of temperature sensitive products or slow migration of moisture and energy recovery in plants where there are simultaneous and comparable requirements of heat and cooling.
Refrigerants
This very important point is presented in the thematic page on refrigeration.