Biomass combustion
Note :
USE OF BIOMASS ENERGY
Introduction
We call biomass all organic materials, mainly of vegetable origin, natural or cultivated, land or sea, produced by chlorophyll conversion of solar energy, fossil fuels excluded.
Biomass is mainly composed of lignin (C40H44O6) (25%) and carbohydrate Cn(H2O)m (cellulose C6H10O5 and hemicellulose) (75%).
Biomass can be converted in energy by three main categories of processes:
biochemical conversion: digestion, hydrolysis and fermentation;
chemical conversion (esterification);
thermochemical conversion: combustion, co-combustion, pyrolysis and gasification.
Biochemical conversion comprises two main types: anaerobic digestion and aerobic digestion.
In the first case, which occurs in the absence of oxygen, there is production of a “biogas”, consisting mainly of methane (50–65%), CO2 (30–35%) and other gases. Reactions take place at temperatures between 20 and 70 °C. The basic reaction is: CH3COOH -> CH4 +CO2
In the second case, there is production of more CO2 and H2O.
Thermochemical conversion is divided into combustion and co-combustion (excess air), gasifi cation (lack of air) and pyrolysis (in the absence of air).
Combustion is the oldest and probably most used conversion mode for both domestic and industrial uses. Its effi ciency is good insofar as the fuel is rich in structured carbohydrates (cellulose and lignin), and especially dry enough (humidity below 35%).
Co-combustion is to simultaneously burn a fossil fuel, usually coal, and biomass (up to 15%) to reduce, in an existing boiler, the amount of initial fuel.
We call the C/N ratio the ratio of the amounts of carbon and nitrogen in biomass. It varies from 10 to about 100. Pyrolysis allows conversion of relatively dry biomass (humidity below 10%) of C/N ratio greater than 30, in various high LHV fuels, storable, gaseous, liquid and solid (charcoal). It takes place at temperatures between 400 and 800 °C, and can be done in several modes: slow pyrolysis or char (solid product only), conventional pyrolysis at moderate temperature (600 °C) (1/3 gas, 1/3 liquid, 1/3 solid), fast pyrolysis at 500–600 °C, which takes place in about one second (70-80% of liquid), fl ash pyrolysis at over 700 °C and in less than one second (more than 80% of liquid).
Gasification of biomass is obtained by performing combustion with lack of air in schematically two main stages: pyrolysis producing gas, liquid and solid phases, followed by the gasification itself of the last two phases.
In a gasifier, the fuel begins by being dried and is then pyrolyzed, these two steps being endothermic. The gaseous products are then burned at high temperature, releasing heat, a part of which is used by the previous two steps. The exhaust gases are then put into contact with the solid phase after pyrolysis and with water from the drying, which causes a reduction reaction which leads to the formation of a synthesis gas rich in CO and H2, whose LHV is approximately 70 to 75% of that of the original biomass.
Several gasification processes exist:
fixed bed systems, which consist of two main technologies, the parallel-flow gasifiers (downdraft), and the counter-flow (updraft);
fluidized bed systems, which consist of three categories depending on the fluidization speed, dense, circulating and entrained fluidized beds.
The first match small or medium facilities, and the latter large ones.
Modeling thermochemical conversion
This section presents a simplified model that can simulate different types of biomass combustion, and in which it is possible to vary with considerable flexibility fuel composition and moisture and combustion conditions. The external class in which it is implemented, called BiomassCombustion , can be used to simulate both a boiler or a downdraft gasifier.
This model is quite simplified compared to those currently being studied in research laboratories, particularly in its representation of pyrolysis (Vijeu et al., 2005). Its main interest is to allow Thermoptim users to approach the study of thermochemical biomass conversion and the insertion of gasifi ers or combustors into complete systems.
To simplify the writing of the model, we took advantage of using the combustion calcul ation functions already present in Thermoptim , just adding equations corresponding to reactions that the software does not take into account.
On the thermodynamics, the main parameters that influence biomass combustion are:
first, of course, fuel composition;
second, moisture, which firstly determines enthalpy required for drying, on the other hand plays on gas composition, and finally influences CO2 dissociation;
finally, quenching temperature and CO2 dissociation rate.
To separate as much as possible the infl uence of these fi rst two parameters, composition is that of dry fuel, and moisture is taken into account by adding water. Given that the overall moisture is not necessarily the one that governs the thermodynamic equilibrium, as part of the steam may not react, for reasons of kinetics or geometry, we introduced an additional parameter, equal to the fraction of water involved in combustion. Physically, this means that a fraction of the water is not dissociated: it must be vaporized but its infl uence on the composition of the gas is the same as if it were inert.
The biomass composition varies widely depending on its origin and humidity. However, we can retain values close to 25% lignin (C40H44O6) and 75% carbohydrates Cn(H2O)m (cellulose C6H10O5 and hemicellulose).
An estimate of the synthesis gas composition and its LHV (values referred to the dry gas) is given in the table below.
[CO] | [H2] | [CH4] | [CO2] | [N2] | LHV MJ/m3N | |
Charcoal | 28-31 | 5-10 | 1-2 | 1-2 | 55-60 | 4.6-5.6 |
12% moist wood | 17-22 | 16-20 | 2-3 | 10-15 | 50-55 | 5-5.85 |
Wheat straw | 14-17 | 17-19 | - | 11-14 | 4.5 | |
Typical estimate | 19-15 | 15-20 | 3-5 | 10-15 | 40-50 | 4.5 |
Definition of fuel and progress of combustion
Fuel definition is made in Thermoptim as follows (Figure below):
dry gas composition, excluding species not included in Thermoptim core, is estimated, for
example in a spreadsheet, and entered in the form of a compound gas (process-point “dry fuel”);
species not considered by Thermoptim core are considered separately: they are entered in the
component screen, and are subject to pre-combustion;
dry gas is mixed with water (H2O gas) to form moist fuel (process-point “humidity”);
final combustion is calculated by core Thermoptim functions, which are emulated from the
external class (external mixer “biomass Combustion”), taking into account pre-combustion and
enthalpy that would have been required to evaporate water.
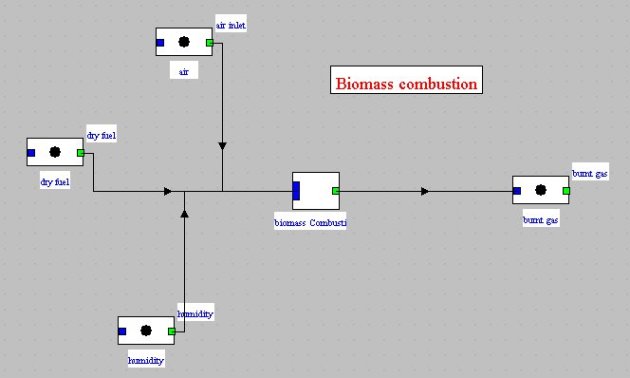
Two examples of use of this component for modeling a biomass boiler and a gasifier are given in Thermoptim model library.
Book reference
Chapter 31 (Part 4)
References
S. P. BABU, Observations on the current status of biomass gasification, prepared for task 33 : Gasification of biomass, 2005
K. W. KWANT, H. KNOEF, Status of gasification in countries participating in the IEA and GasNet activity, 2004
L. VAN DE STEENE, G. PHILIPPE, Le point sur la gazéification de la biomasse, Bois-Energie n°1, 2003
VIJEU R., GERUN L., BELLETTRE J., TAZEROUT M., YOUNSI Z., CASTELAIN C., Modèle thermochimique bidimensionnel de pyrolyse de la biomasse, International Congress on the Renewable Energies and the Environment - CERE, 24-26 mars 2005, Sousse, Tunisie, 8 p.